The 3D hot-bent glass manufacturing process has high requirements for the temperature control accuracy and response speed of the heating system.The heating tubes need to be combined with dedicated temperature control equipment to achieve heat zone control,process temperature range distribution and heating stability guarantee.The temperature control matching structure directly affects the glass forming yield and energy consumption efficiency.
3D heat-bent glass heating tubes are typically composed of resistance wires or ceramic heating elements and are installed on heating platforms,heat-bent furnace chambers,negative pressure table surfaces,and other parts through curved surfaces or mold bonding.To achieve precise temperature control,a closed-loop system needs to be formed by integrating thermocouples,temperature controllers,PID regulators,solid-state relays,etc.
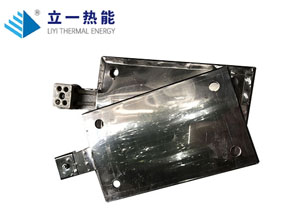
Temperature control equipment is mainly divided into single-point temperature control and multi-section temperature control.Single-point control is suitable for constant temperature conditions.Local temperature feedback is collected through a thermocouple,and the target temperature is set in conjunction with a digital temperature controller to drive the on-off switching of the heating tube.It is suitable for equipment structures with a small range of hot bending and little temperature fluctuation.
The multi-zone temperature control system divides the heating zone into multiple independent zones based on the shape of the glass and the requirements of the thermal bending cycle.Each zone is equipped with independent sensors and control circuits to achieve local compensation and regulation.This method is suitable for the process requirements of irregular-shaped glass,large curvature variations,and high precision of the formed window.
In terms of control accuracy,the temperature control instrument can set the heating rate,constant temperature time and cooling process,and match different glass thicknesses and processing techniques.The power size and layout density of the heating tubes are determined by the temperature control strategy,which can achieve overall uniform heating or local high-temperature enhancement.
When used in conjunction,the system needs to be equipped with functions such as over-temperature protection,abnormal current alarm,and self-check for temperature zone loss of control to ensure the safe operation of the equipment.Some hot bending equipment also supports the integration of PLC control systems and remote setting through human-machine interfaces.